Pinch Valves: An Uncomplicated Valve With an Important Purpose
Used in on/off or throttling applications, choosing the right style pinch valve depends on the application.
#basics #knowyourvalves
Pinch valve designs are generally simple, employing an elastomeric tube forced together or pinched to stop the flow of media. This pinching force can be applied in a few ways: compressed air or fluid can be supplied directly into the valve housing to force the elastomeric tubing to close, or a mechanical clamp can be used that is closed via a manual handle or an actuator.
Pinch valves are used in on/off applications as well as throttling services. They are used in applications from clean or sanitary services such as the chemical, food and pharmaceutical industries to more industrial services such as wastewater, the cement industry and systems with a high concentration of bulk solids. Pinch valves are used in sanitary services for their cleanliness and in more industrial services because of their low friction and resistance to clogging. They do well in these services compared to other more common valve types such as butterfly, ball and globe valves because their simplicity and previously named benefits make them cost effective.
PINCH VALVE STYLES
The different types of pinch valves can be described broadly as two types: those where the sleeve is integral to the body and those where a separate clamp is used to pinch a tube or a hose closed.
Integral Sleeve
A pinch valve with an integral sleeve through the valve body can be actuated by compressed air or hydraulic pressure applied into the valve body between the body and sleeve. As the air or hydraulic pressure fills the body cavity, the pressure closes off the sleeve to restrict or stop the flow of media. These valves may also have a mechanism that closes via a manual operator or actuator integral to the valve. This style of pinch valve can be used as a control valve when a mechanism is used to close the valve.
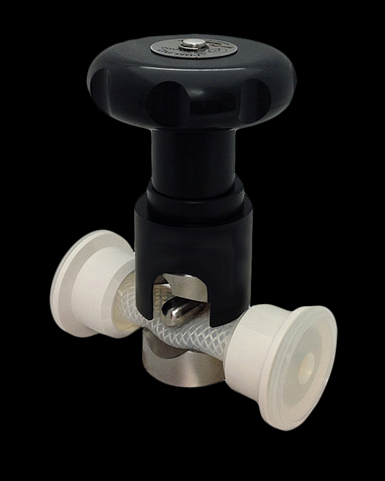
Manual pinch valve with safety cover lifted to show hose compression.
Source: IMI PBM
Pinch valves are generally very low maintenance. When maintenance is required, it most often involves the elastomeric tube or hose because that is what is being forced or clamped to restrict or stop flow. When the sleeve, tube or hose becomes worn or damaged from use, it must be replaced. Meanwhile, because the valve body components are isolated from valve media, they require little maintenance.
Pinch valve components can be made from a variety of materials, depending on the severity of the service and the media that flows through the valve. The sleeve, tube and hose can be made from neoprene, natural rubbers, silicone, EPDM (ethylene propylene diene monomer rubber — an extremely durable synthetic rubber membrane that has a higher heat resistance than natural rubbers), FKM (fluoroelastomer, which has more heat and chemical resistance than nitrile or neoprene) and many other elastomers. The valve body can be made of plastics, stainless steel, aluminum and other metals, depending on where the valve will be used.
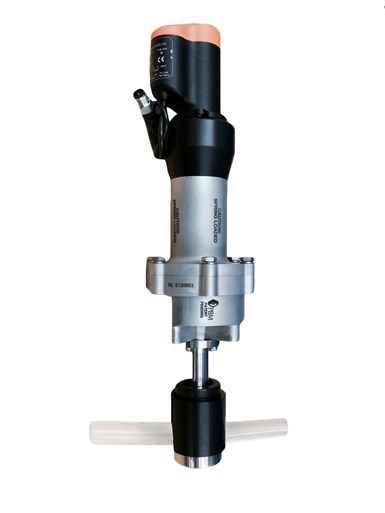
Source: IMI PBM
Actuated pinch valve with limit switch.
Integral sleeve-style pinch valves are chosen when the media can be corrosive or when it contains solids or abrasives. This is because there is minimal friction within the sleeve of the pinch valve, so it is resistant to clogging. These valves also may be chosen when minimal turbulence is required or in cases where excellent drainage is necessary. Pinch valves are also an excellent choice when media exposure to nonelastomeric materials can be an issue such as when the media is corrosive to metals.
Clamp Style
The clamp-style pinch valve essentially compresses a separate tube or hose closed using a manual actuator, pneumatic actuator or solenoid actuator that exerts the clamping force to provide shutoff. This style of pinch valve is completely separate from the tube or hose. It can be installed and removed from the system without disassembling the hose system or breaking the line. This type of pinch valve is designed for systems where breaks in the process tubing or hose are not feasible. In most cases, these valves are used as a clamp for single-use tubing.
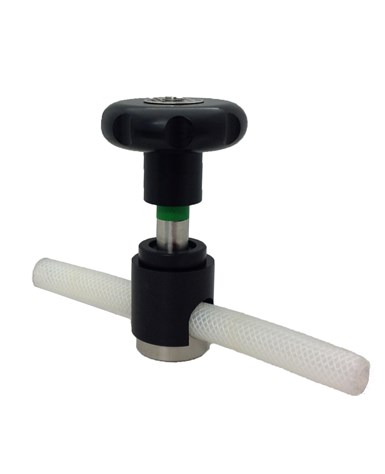
Manual pinch valve in the open position (no hose compression).
Source: IMI PBM
Because the clamp-style pinch valve is separate from the tubing or hose that it closes off, the valve itself requires minimal maintenance. This style of pinch valve is generally made from metallic materials such as stainless steel or aluminum, with handles made from plastics to help reduce weight. In some cases, this style of pinch valve can be made entirely from plastic to reduce cost and weight. However, doing so creates a more limited ability and life span.
Clamp-style pinch valves are chosen for services that require a valve to be installed with no process break. They are generally installed on single-use disposable systems, in pharmaceutical manufacturing, and in food and beverage applications that use flexible or braided tubing.
CONCLUSION
Although pinch valves have a simple design and purpose, they are used for a wide variety of applications. Knowing their purpose and how they work enables those who choose them to pick the right type.
This article was published previously and has been updated by Jeff Kerr, IMI PBM.
RELATED CONTENT
-
Valve Basics: Plastic Valves
Polymer materials of construction expand capabilities of valves for specific applications.
-
Pressure relief valves: What makes them different?
Facilities use many different types of valves to keep themselves operating, and each valve within a plant serves a different function.
-
Pressure Relief Valve Basics – Spring-Loaded Safety Relief Valves
Learn for the first time or brush up on this common valve product.